We collaborated with the Manufacturing Technology Centre (MTC) to construct, manufacture and test two sandpit buildings which provide a safe space for conceptualisation, learning and development to drive innovation and growth in the construction industry.
This research and development project was a key part of the Construction Innovation Hub’s platform design programme, funded through Innovate UK’s transforming challenge. The key aim of the programme was to drive efficiency into the construction sector, reducing costs and improving quality and whole life value, by adopting a manufacturing-led, platform-based approach to construction. The sandpit programme, which saw MTC partnering with Balfour Beatty and its supply chain partners to push the boundaries of platform construction and offsite construction techniques, delivered two demonstrator buildings that could be viewed as portions or ‘slices’ of how future buildings could be delivered faster, better and greener.
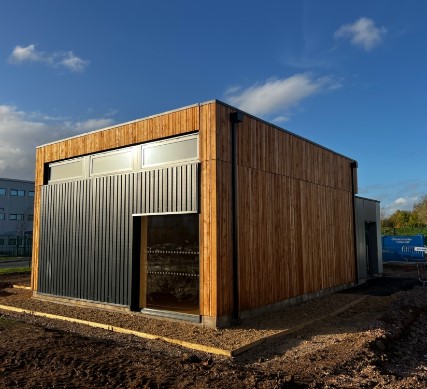
These sandpits have helped demonstrate that by using a manufacturing approach, we can deliver outcomes that will reduce cost, carbon and waste as well as improve productivity, safety and quality. They also have an on-going aim to provide a safe, neutral environment to develop and functionally test new product offerings within a platform setting, lowering the barrier to entry for new market entrants.
By scaling up these initiatives, we can unleash a wave of creativity and collaboration that will reshape the future of construction and bring about substantial benefits for society. It has the potential to drive efficiency, improve quality, sustainability and innovation, ultimately paving the way for a brighter and more advanced built environment.
demonstrator buildings
days to assemble and install a pre-cast concrete frame
time saving on-site through use of laser cut reinforcement
Healthcare sandpit
The healthcare sandpit follows the success of University College London’s ‘Challenging Space Frontiers in Hospitals’ programme. The purpose of the sandpit is to act as a test-bed for a standardised set of building systems and components that can be used in various configurations of room clusters, based on the UCL concept design.
The team focused on constructing a room that serves as an interventional therapy suite (a theatre for minor operations), but could also be used, with minimal adaptation, for interventional critical care or as an isolation room. As one of the hospital’s more complex rooms for services, successfully demonstrating a component approach for this space opens the door to easily applying the same methodology to less complex rooms. One main aspect was developing the design, manufacture and install the mechanical, electrical and plumbing (MEP) systems.
Key highlights of this approach include:
Modular module for MEP services designed and efficiently installed on-site within a single day:
- Enhanced flexibility: seamless replacement or reconfiguration of MEP elements, allowing for greater adaptability to changing requirements.
- Streamlined through standardisation: reducing complexity, easier to install and ensures consistency in implementing MEP services across various rooms.
Pre-cast concrete frame:
- The pre-cast concrete frame was installed and assembled on-site within a short timeframe of four days.
- Laser-cut reinforcement is incorporated into the concrete frame, ensuring more efficient and accurate placement of reinforcement materials. Also, safer to manufacture and install as there are no sharp edges than traditionally cut rebar.
Laser-cut reinforcement:
- Precision engineering resulted in higher quality compared to standard bar reinforcement methods.
- 166% time saving on-site through use of laser cut reinforcement vs traditional methods.
- Installation time reduced from four hours to build and place two cages to one hour to place four cages, plus two hours to cut and adjust.
- Valuable lessons learnt, providing insights for future optimisation (i.e. using less material than existing methods) and improvement.
Education sandpit
Building upon the successful GenZero program by the Department for Education, the education sandpit project offered an exciting opportunity to expand on the achievements of the GenZero demonstrator showcased at COP 26 in Glasgow. The focus was on developing the next generation of sustainable school design through the combination of volumetric and panelised MMC techniques.
Our remit was to deliver various large-scale components, including a volumetric pre-manufactured toilet pod, a small studio constructed with homegrown-engineered timber panels, and an adjacent volumetric corridor that provides access to these spaces. Each volumetric component is fully integrated and structurally independent, allowing for easy transportation via road.
This sandpit project aimed to create a model for sustainable and resilient school buildings that meet the needs of future generations, while minimising environmental impact.
Key features included:
- Low maintenance materials: ensuring durability and reduces the need for frequent maintenance.
- Low/zero carbon systems: helps minimise carbon emissions and promote energy efficiency.