As part of Europe’s largest infrastructure scheme at the time, we worked in joint venture with BeMo Tunnelling, Morgan Sindall and VINCI Construction to deliver early access shafts and sprayed concrete lining for the station tunnels.
Whitechapel – a key interchange hub
The Elizabeth Line (previously known as Crossrail) is a major new rail link project designed to provide a world-class, affordable railway. It will provide a high-frequency, convenient and accessible service that connects the City, Canary Wharf, the West End and Heathrow Airport to commuter areas across London.
Complex construction
The major construction works for the project included the construction of the Whitechapel and Liverpool Street station SCL tunnels.
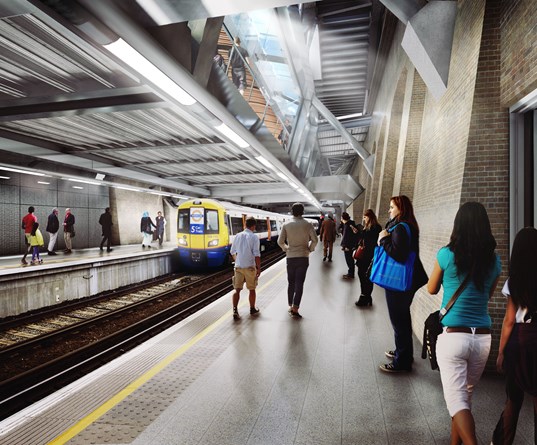
Associated works included the shafts and adits, platform tunnels, Tunnel Boring Machine (TBM) reception chambers and launch chambers, cross passages, access passages, escalator barrels, ventilation ducts and a link passage from the new Liverpool Street station to the London Underground Northern Line in Moorgate station. The works also included the construction of four compensation grouting sites in the vicinity of Liverpool Street station and one compensation grouting shaft in the vicinity of Whitechapel station.
Realising the benefits of off-site construction
Over 259 horizontal distribution service modules comprising of heating, chilled water, water services and containment were manufactured and installed by our in-house team. This removed over 11,000 hours of work from site, reduced working at height requirements and improved quality.
Award-winning innovation
Whitechapel is one of Crossrail’s most ambitious new stations, but it is also one of the most challenging, with a raft of improvements being delivered in a tightly-constrained and highly-populated area. In order to deliver the works, the Balfour Beatty, BeMo Tunnelling, Morgan Sindall plc and VINCI Construction joint venture employed various innovative solutions. These included the bespoke ‘Uphill Excavator’, which enabled construction of the shafts from the bottom up, much earlier and more safely than would have been possible with traditional downhill methods.
The approach was recognised as a game-changing innovation with the award of the Product Design Innovation accolade at The British Construction Industry Awards in 2015, as well as receiving the Technical Design of the Year and Product and Equipment of the Year awards at the 2015 NCE Tunnelling and Underground Space Awards.
Service modules manufactured offsite
Hours of work removed from site