The £42 million, 32 storey development provides 450 student beds at the centre of One Nine Elms in Vauxhall, London is state-of-the-art accommodation will provide students with features such as fast broadband and under floor heating.
New area development
The project involved the design and construction of a 32-storey student accommodation tower with a reinforced concrete frame built using a slip form. Situated within walking distance of Vauxhall mainline rail station, the site is surrounded by a hub of pre-construction and construction activity, including the site of the new American Embassy.
The exterior of the building is covered in a unitised brick slip cladding system façade sourced from Austria. We have also supplied and installed the furniture, fittings and equipment, which are similar to those installed on the 199 Westminster Bridge Road scheme, and in keeping with the client’s brand.
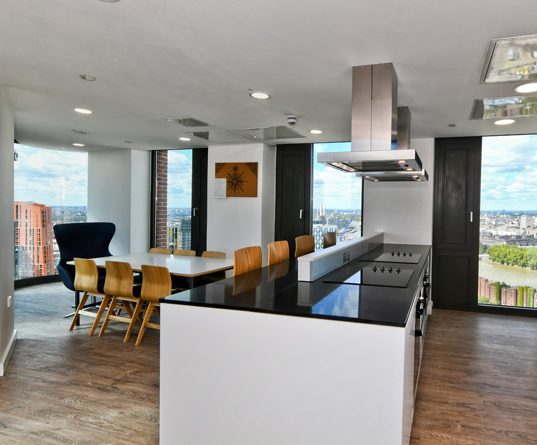
Working in a constrained site
The 5 Miles Street footprint is triangular and confined, measuring some 30 by 40 metres to give an overall footprint area of approximately 1,000m². The eastern site boundary is a Network Rail masonry viaduct carrying the mainline railway to and from Waterloo station.
Due to these site constraints, we worked closely with the façade supplier to devise a lightweight unitised panel system which reduced the weight of the panels, making the installation process faster and more efficient. The system was installed with the use of a mini-crane positioned on the building floor plates, eliminating the need for a tower crane to lift the panels.
footprint
student beds
work placement opportunities
Modern methods of construction
To help with collaboration, our team worked closely with customer and supply chain partners at the early stages of the project to discuss the construction methodology and key deliverables, optimising the design and programme to minimise the risk of delays or costly rework.
Modular construction methods were used throughout the project, including bathroom pods and other prefabricated elements such as booster and pump sets. This approach to the development has increased the speed of construction and improved quality.
It was a requirement that all mechanical and electrical materials required to complete the works in a single room were packaged together and delivered to their final destination. This approach also saved installation time on site as all quality and assurance checks on components were undertaken prior to the items arriving on site.