Our Zero Carbon Construction Site Diary
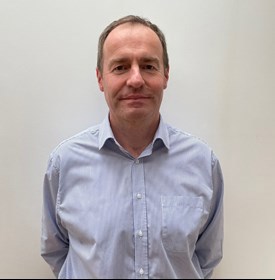
When we started looking at getting as close to zero carbon as we could on this site, we knew that more resource would be needed than on a standard site, as it doesn’t yet fit in our ‘business as usual’ approach. It calls for disruption to the way we normally operate and is making us look afresh at our processes, how and what we procure, and what we’re measuring. The conversations we’re having now are taking time and energy we don’t usually need on a standard project, as we look further afield for equipment and consider the art of the possible through the zero carbon lens. To mitigate this, zero carbon needs to be part of the conversation as early as feasibly possible. The longer it is left out the conversation with the customer, designers and supply chain, the more disruptive it is and the more resource needs to be allocated.
We realised we would need a new body to help coordinate the resource and expertise from across our UK business, so we set up a Delivery Group to do this and to oversee and document the decisions being made, as we outlined in our Roadmap. We’ve also recognised that we need additional Procurement resource so we can assess all the options and speak to supply chain partners about what’s available; and that we need a Net Zero Champion and a Carbon Manager to accurately calculate and record the carbon impact and help guide some of the decision-making with expert knowledge about what the different options mean for our emissions. These extra resources are all now in place or being put in place and will allow us to push forward with low carbon solutions as well as capture and pass on the learnings from this scheme in detail to our other projects.
Our view is that this extra resourcing should come down for others as we roll out the lessons we’re learning and the innovations we’re developing on this site, and as the equipment, goods and materials become more readily available, so we’re treating it as an investment.
On site
At the moment, the focus on site is on Advance Works set up. The standard site set up process we use as part of every site mobilisation already uses our Power Profiler to determine the most efficient cabins to use and that’s what we’ve chosen on this occasion. They cost more to hire in per week / month, but they save on both carbon emissions and fuel costs, so over the long term, it works out more efficiently and more sustainable. We are not passing on these higher upfront costs to our customer.
We’ve chosen a standalone Solar Hybrid WC Toilet Unit and a further two other STANDARD units providing office, canteen and drying space, powered by a Solar Pod 30 Generator to reduce emissions. These options are not very common on sites and this is certainly the first time we’ve used a solar toilet in our operations Scotland, so it’s new tech for our site team. Powered by roof mounted solar panels, with a generator for back up, the toilet unit delivers a 95.5% reduction in both emissions and in terms of noise pollution.
Although we’ve already used solar-hybrid generators in Inverness and, outside Scotland, on our Viking Link interconnector scheme in the Midlands, we were initially unsure about using solar power in Scotland, where the climate is generally cool and wet. The team have been pleasantly surprised. The units have been a success and have already proven their value although there have been other lessons we’ve learnt. For example, the space required for the solar-hybrid is significantly greater than for a traditional generator. This meant that, given the space had been pre-allocated for standard unit sizes, we were not able to position them in a fully south-facing direction which provides maximum power. This, again, highlights the importance of planning ahead for the most efficient options in order to ensure we have the space to maximise solar generation, but also shows that this technology is only really workable for smaller construction sites, due to the extra space needed.
We plan to install longer-term site accommodation that has greater energy efficiency that comes from double glazed windows with inert gas fill-in and heat reflective coating, less power intensive heaters with digital thermostat and 41% improvement to insulation in the roofs, walls and floors. These are our EcoSense cabins, an industry first, designed through collaboration between Balfour Beatty, our supply chain partner and the UK manufacturers. The state-of-the-art Econet system Balfour Beatty has developed in collaboration with Sunbelt and Invisible Systems will be installed to this site accommodation to reduce carbon emissions by up to 80%. EcoNet is configured to autonomously manage power demand by automatically turning appliances and equipment off when not in active use. This helps to regulate power consumption during times when demand is highest, such as when site compounds are fully occupied, equipment is being operated and appliances, such as drying rooms and heaters, are in use.
Heavy plant
One of the difficult decisions we’ve had to make already has been over the excavator needed for the site. Ideally, we would have liked to use an electric or hydrogen excavator, however these only exist as 1.9 tonne mini-excavators, as the batteries aren’t big enough to power the heavier models.
Next, we looked at a hybrid excavator – diesel with a backup battery. These are still comparatively limited in number and as the cleanest option available on the market are in very high demand. Unfortunately, at the time we needed to source it, there were none available – many of those on the market are already in use on the HS2 scheme, which has ambitious environmental specifications. At this point, we looked at an excavator which complies with the Euro V engine standard, which places rigorous limits on pollutant emissions, in particular nitrogen oxides (NOx) and particulate matter (PM). While this is still modern plant and complies with all of our minimum environmental and safety standards, it isn’t the excavator we would like to have used. Unfortunately, we have found that the lowest emission heavy plant simply isn’t available in the same numbers as standard heavy plant. Until this changes, we’ve realised that we need to plan far further ahead in order to ensure we are able to secure them. However, this experience has also resulted in another interesting internal conversation around the wider circular economy piece: it isn’t actually the most sustainable option to keep buying new plant and discard the older models as new technology comes online. Retrofitting older models and bringing them up to a higher standard can ensure that they are meeting higher emissions standards while ensuring that they are usable for their full lifespan of 10-12 years.
Key learning |
Our action |
A zero carbon construction site needed to be part of the conversation as early as possible with the customer, designer, and supply chain |
Learning filtered back to the rest of the business. |
More time and resource are needed up front to examine all the options and assess their carbon impact. |
We have put in place a Delivery Group to oversee the decision-making process and corral expertise from across the UK businesses. The procurement resource has also been increased specifically for this scheme. A new Net Zero Champion and Carbon Manager have been put in place. |
Solar-hybrid is definitely something that we can be confident about using on site. However, it takes more space than standard generators, which needs to be planned for from the beginning and which also limits their use to smaller sites. |
Learning filtered back to the rest of the business. |
Until there is more available as standard, we need to plan further ahead to secure the most carbon efficient heavy plant than we would do with standard machinery. |
Learning filtered back to the rest of the business. Discussions ongoing about the use of retrofitted heavy plant and what our hierarchy of carbon efficient plant should look like, taking circular economy considerations into account. |
If you have observations or queries on the points outlined in this entry, please contact: Veena.Hudson@balfourbeatty.com.