In our new ‘Five minute read’ series, Balfour Beatty experts share their perspectives on important topics within the construction and infrastructure industry, discussing opportunities for the sector and sharing views on how we can increase awareness.
Modern Methods of Construction (MMC) techniques in the construction and infrastructure industry offer a major opportunity to enhance project efficiency and transform the industry.
Major projects like HS2 and Hinkley Point C are already using prefabricated modular segments, and there is a growing interest in expanding MMC practices to construct hospitals, schools, and housing. The key principle is that by adopting a manufacturing from the beginning of a project, construction teams can minimise on-site work, allowing them to focus on the intricate and unique aspects of each specific project, bringing transparency to every step in the delivery cycle, using digital tools developed internally by engineers working in close collaboration with software specialists.
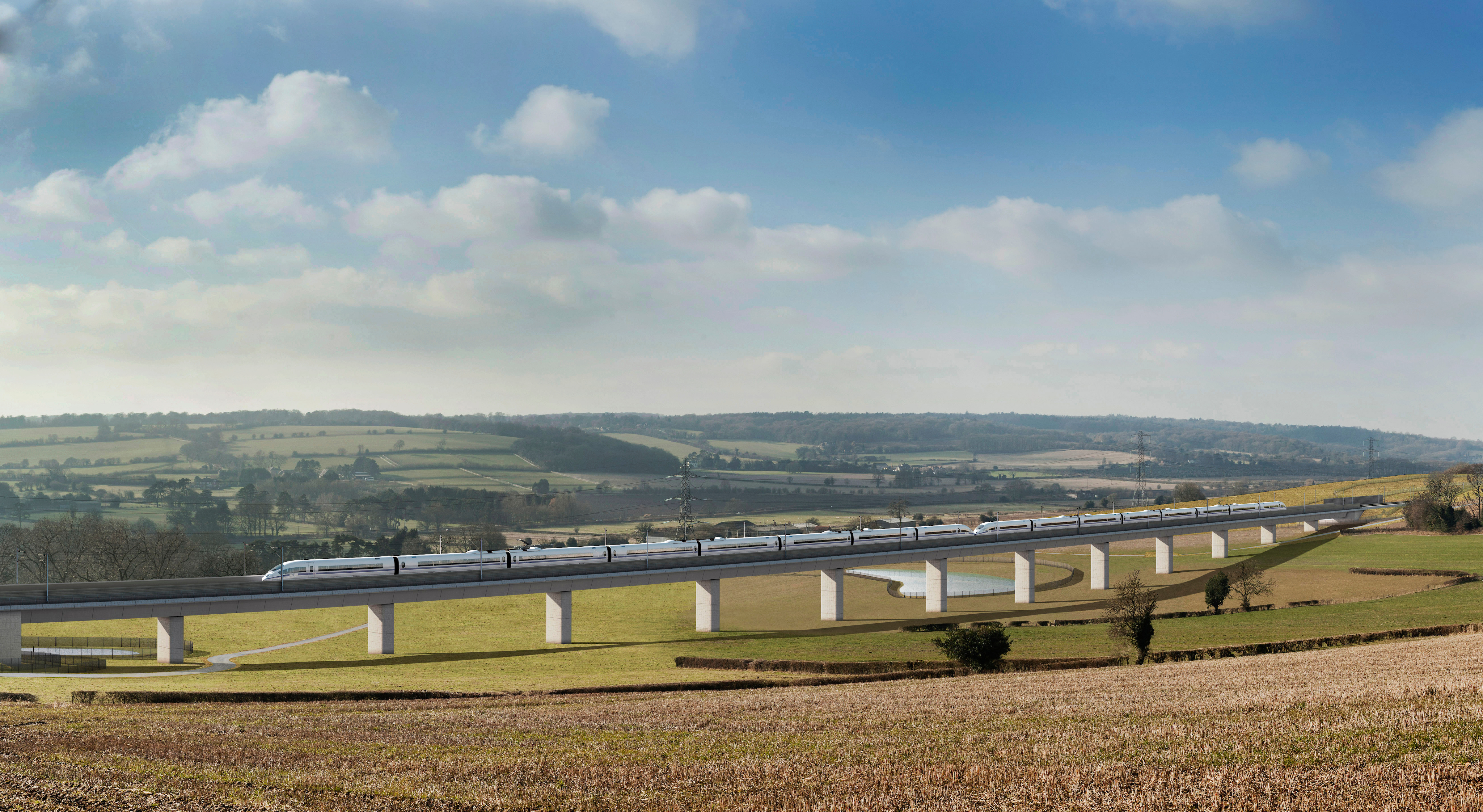
The automotive industry has already made significant progress in this area by emphasising standardisation. For instance, VW, SEAT, Audi, Skoda, and Porsche share 70% of platform components, while the remaining 30% encompasses distinctive features and finishes that differentiate their products. Government-supported preliminary research showed that approximately 38% of components could be shared across various sectors such as Transport, Health, Defence, Education, and Justice, mirroring the efficiency achieved in the automotive industry.
However, the full benefits of MMC will only be realised if the entire sector embraces it, which will require cultural and structural changes across the industry.
Key factors for successful MMC adoption include:
Adopting a production mindset
Design decisions must be finalised before production begins, avoiding costly changes during construction. Components cannot be altered once they leave the factory to ensure cost, safety, and quality.
Earlier involvement of key parties
All stakeholders, including designers, manufacturers, logistics, and assemblers, should be involved early to incorporate factory-specific requirements. Careful planning from the beginning is necessary to avoid contract and supply chain pressures due to longer MMC lead times.
Demand-led change
The government, as the largest construction client, plays a crucial role in driving MMC adoption. Creating a stable pipeline of MMC projects encourages investment and attracts private investors. Publishing an MMC strategy on design standardisation is also essential.
Sector-wide culture change
Shifting from a project-based approach to a product-based approach is necessary for MMC to disrupt the construction sector positively. Product-based manufacturing supply chains require longer-term, stable demand. The Government can drive this cultural change.
New skillsets
Investment in new skillsets is crucial to harness the potential of MMC and address industry skills shortages. Skills such as manufacturing mindset, system design integration, logistics, and digital delivery strategies need to be developed industry-wide.
Building supply chain capacity
Contractors need integrated relationships with designers and manufacturing supply chains to support delivery and ensure end-to-end quality management. Investment and understanding of capacity, both nationally and internationally, are necessary to meet growing MMC demand.
MMC-supportive procurement routes
Existing procurement models should adapt to accommodate MMC cost distribution, including front-loading large orders for material manufacturing. Assessing value and allocating risk is crucial in selecting the right MMC solution.
MMC has the potential to transform the construction and infrastructure industry, align with government priorities, and improve productivity, skills, and emissions. To achieve these benefits, reducing barriers to MMC uptake, deepening supply chain collaboration, creating a demand pipeline, and improving the commercial viability of MMC adoption are essential for both the government and the sector.
Balfour Beatty and MMC
Balfour Beatty is at the forefront of adopting MMC approaches in project delivery. We leverage platform solutions, invest in digital tools, and focus on staff development to instil a manufacturing mindset in our engineers. Embracing manufacturing-based construction solutions is helping us to reduce project timelines, minimise waste, and improve overall delivery, while data-driven decision making enables us to achieve game-changing efficiencies and introduce new ways of working. This streamlines processes, cuts costs, and optimises project delivery and positions us to seize opportunities as the sector transforms.
Through MMC, we are also tackling traditional industry challenges such as skills shortages, rising costs, and productivity constraints. Our portfolio includes successful showcases of off-site manufacturing in various projects, from residential buildings and student accommodation to major ventures like Hinkley Point C.
Download a copy of our Modern Methods of Construction document here.
Read more in our case studies:
Large scale projects require in-depth logistics planning to enable efficient and safe working. On Hinkley Point C tunnelling and marine works, we deployed a systematic approach to delivering the concrete segments for the tunnels from our Avonmouth factory to site. Delivery vehicles carrying the precast segments were assigned a designated timeslot, and if they do not arrive within five minutes of their slot they are denied entry to site.
To achieve this level of accuracy in delivery timings, a digital supply chain platform is used to plan the deliveries. The platform ensures the timings of deliveries are realistic and all required information, such as the vehicle’s registration and the load it is taking to or from site, is provided ahead of the delivery slot. Using this tool mitigates key operational risks including multiple deliveries arriving at the same time which would compromise the ability of the site team to work safely.
A vital part of the NHS Trace and Test network, we constructed the Rosalind Franklin Laboratory - a world-class facility capable of processing thousands of tests every week and playing a critical role in in the UK’s response to the COVID-19 pandemic.
Our in-house mechanical and electrical specialists, Balfour Beatty Kilpatrick, worked closely with our customer to design and manufacture 263 prefabricated modules of varying sizes for the laboratories. Containing pipework, ventilation ductwork and cable management systems, the modules were manufactured off-site, ready to be quickly installed on-site.
Adopting modern methods of construction such as off-site manufacturing and modularisation, enabled us to successfully complete the project within the reduced timescales whilst driving improvements in safety and quality and reducing waste.
Our 50:50 joint venture, Gammon, is constructing the world’s largest student halls at City University of Hong Kong in Ma On Shan using modular integrated construction (MiC).
The new hall of residence consists of six buildings ranging from 13 to 18 storeys and will provide over 2,000 residential units. By adopting a MiC approach, re engineering the foundation design, and overlapping foundation and superstructure works, it is expected that the construction programme will be reduced.
With MiC, a total of 1,344 prefabricated components will be manufactured off-site, reducing noise and waste at the site by 75% and 68% respectively.
In a huge feat of engineering, Balfour Beatty VINCI delivered the world’s longest box slide to move HS2’s 12,600 tonne bridge into place over the M43 in Warwickshire.
An innovative construction method was utilised by the project team to build a 12,000-tonne box-frame bridge structure on land adjacent to the motorway and then glide it into position over 165 metres using a high-tech raft. This resulted in only two one-week closures of the motorway over a 12 month period, dramatically reducing the impact on road users and on local communities.
The operation took 40 hours at speed and was delivered during a 10-day motorway closure during Christmas, with all works completed ahead of time.
To deliver the $1.6 billion Penn Pavilion hospital efficiently, Balfour Beatty, as part of the PennFIRST team collaborated with project partners and our customer to develop a lean manufacturing-based approach to construction.
This approach saw the project become the first in Philadelphia to construct mechanical racks and 504 bathroom pods off-site. To make this possible, we played an integral role in standardising the building’s structural floor plate and interior design early in the project, which enabled an efficient and effective prefabrication approach to be deployed.
Working closely with our project partners, we maintained and operated a 60,000-square foot warehouse, located two miles from the job site, where three primary building elements: mechanical racks, bathroom pods and zone valve boxes were prefabricated. On a project of this magnitude and complexity, a streamlined design yielded tremendous benefits within a lean prefabrication strategy.
The team standardized the patient floor to only two patient room designs. This achieved enhanced efficiencies via the reduction in total jigs and templates needed for manufacturing.
To help us deliver the £1.2 billion Terminal 2 Expansion Works project at Hong Kong’s International Airport right first time, we have deployed cloud- based visual collaboration software to help with tracking and design coordination during the project’s construction phase.
The software enables all stakeholders to communicate their designs in real-time within a navigable 3D environment based on the project’s Building Information Modelling (BIM) data. With a user-friendly interface, including multiple dashboards and notifications on-demand, the software provides improved accessibility and efficiency in the coordination and identification of issues.
All updates to the designs are uploaded every 24 hours, ensuring trust in the data and creating one source of truth for the project team to work from.